Average cost of installing an inground outdoor pool? It’s a question many dreamers of backyard oases ponder. The price tag can vary wildly, depending on factors like pool size, materials, and location. This journey into the world of inground pool installation will unravel the complexities of budgeting for your personal aquatic paradise, exploring everything from initial design to the final splash.
From the initial design phase to choosing the right contractor, many variables influence the final cost. We’ll break down the expenses associated with materials (concrete, fiberglass, vinyl), labor, permits, and unexpected additions. Understanding these components allows you to create a realistic budget and avoid costly surprises along the way. We’ll also examine timelines for different pool types and offer tips for navigating the permitting process.
Factors Influencing Inground Pool Costs
Building an inground pool is a significant investment, and the final cost can vary considerably depending on several factors. Understanding these factors is crucial for budgeting effectively and managing expectations throughout the project. This section will break down the key elements that influence the overall price.
Pool Size, Shape, and Materials
The most fundamental determinants of cost are the pool’s dimensions, shape, and the materials used in its construction. Larger pools naturally require more materials and labor, driving up the price. Complex shapes, such as free-form designs, also increase costs due to the increased labor involved in excavation and construction. Material selection significantly impacts the price; concrete pools, for example, are generally more expensive than vinyl-liner pools due to the higher cost of materials and the more extensive labor required for construction.
Types of Inground Pools and Price Ranges
Three main types of inground pools dominate the market, each with its own price range:
- Concrete Pools: These offer the greatest design flexibility and durability but are typically the most expensive, ranging from $50,000 to well over $100,000 depending on size, features, and location. The high cost reflects the labor-intensive nature of the construction process, including specialized concrete work and finishing.
- Fiberglass Pools: Pre-fabricated fiberglass pools are generally more affordable than concrete, usually costing between $30,000 and $80,000. Their quicker installation time and lower labor costs contribute to their lower price point. However, design options are more limited compared to concrete.
- Vinyl-Liner Pools: These are typically the most budget-friendly option, with prices ranging from $20,000 to $50,000. The lower cost is due to the simpler construction process involving a pre-formed liner installed within a framework. Durability is generally less than concrete or fiberglass.
Impact of Location on Installation Expenses
Geographical location plays a substantial role in the overall cost. Factors such as accessibility of the installation site, local labor costs, permitting fees, and the availability of materials all influence the final price. Pools installed in remote areas or locations with difficult terrain will typically be more expensive due to increased transportation costs and labor challenges. Areas with high labor costs will naturally result in higher installation expenses.
Furthermore, differing local regulations and permitting processes can add to the overall cost. For example, a pool installation in a mountainous region might cost significantly more than a similar project in a flat, easily accessible area.
Cost Implications of Various Pool Features
The inclusion of additional features significantly impacts the total cost. The following table provides a general overview of the cost implications of various common features:
Feature | Low-End Cost Estimate | Mid-Range Cost Estimate | High-End Cost Estimate |
---|---|---|---|
Heating System (e.g., heat pump) | $3,000 | $6,000 | $12,000+ |
Water Features (e.g., waterfall, spa) | $2,000 | $5,000 | $15,000+ |
Decking (e.g., concrete, composite) | $5,000 | $10,000 | $25,000+ |
Lighting (LED or other) | $1,000 | $2,500 | $5,000+ |
Automatic Pool Cover | $2,000 | $4,000 | $8,000+ |
Labor Costs and Installation Timelines
The cost of labor for inground pool installation is a significant portion of the overall project expense, often rivaling or exceeding the cost of materials. Understanding these costs and the associated timelines is crucial for realistic budgeting and project planning. Several factors influence the final labor bill, leading to a wide range of potential outcomes.Labor costs for inground pool installation typically range from $20,000 to $60,000 or more, depending on several key factors.
This wide range reflects the variability in project complexity, geographical location, and the contractor’s experience and overhead. It’s essential to obtain multiple detailed quotes from reputable contractors to get a clear picture of the labor costs in your specific area.
Factors Influencing Labor Costs
Several factors significantly impact the labor costs associated with inground pool installation. Project complexity, for instance, plays a major role. A simple, rectangular pool in level ground requires less labor than a complex, freeform design with intricate features like waterfalls, spas, or tanning ledges. The location of the project also influences labor costs. Accessibility to the installation site, the need for extensive excavation or grading, and even local labor rates all contribute to the final price.
The contractor’s experience and reputation are also important considerations; more experienced contractors may charge more, but their expertise can minimize delays and potential problems. Finally, the chosen pool type (concrete, fiberglass, or vinyl-liner) affects labor requirements. Concrete pools generally demand the most labor due to their custom nature and on-site construction.
Average Installation Timeframes
The average installation timeframe varies considerably depending on the pool type and project complexity. Simple, pre-fabricated fiberglass pools might be installed within a few weeks, while custom concrete pools can take several months. Vinyl-liner pools often fall somewhere in between. Weather conditions can also significantly impact timelines, causing delays due to rain, extreme temperatures, or frost. For example, a straightforward fiberglass pool installation in favorable weather conditions could be completed within 2-4 weeks, whereas a large, complex concrete pool with extensive landscaping might take 4-6 months or even longer.
Key Stages of Inground Pool Installation and Time Commitments
Understanding the key stages and their associated time commitments provides a better perspective on the overall installation timeline. The actual duration of each stage can fluctuate based on the project’s size, complexity, and unforeseen challenges.
- Site Preparation and Excavation: This initial phase, involving surveying, grading, and excavation, typically takes 1-3 weeks, depending on the size and complexity of the pool and site conditions. This includes removing topsoil, digging the pool hole to the correct dimensions, and preparing the base.
- Pool Shell Installation (for fiberglass or vinyl-liner pools): This stage involves setting the pre-fabricated shell into the excavated hole and ensuring proper leveling and positioning. It generally takes 1-2 days for fiberglass pools and 2-3 days for vinyl-liner pools, depending on the size and shape.
- Plumbing and Electrical Work: The installation of plumbing lines for the filtration system and any other water features, along with electrical wiring for pumps, lights, and other equipment, typically takes 1-2 weeks. This includes connecting all the necessary components and ensuring everything is properly grounded and waterproofed.
- Concrete Work (for concrete pools): This is the most time-consuming phase for concrete pools, involving forming the shell, pouring and finishing the concrete, and curing the concrete to achieve adequate strength. This can range from several weeks to a month or more, depending on the size and design of the pool.
- Finishing and Landscaping: This final phase encompasses the installation of coping, decking, tiling, and landscaping. This can take several weeks to complete, depending on the extent of landscaping work and the complexity of the finishing elements.
Material Costs
The cost of materials significantly impacts the overall price of your inground pool. Choosing between different materials—concrete, fiberglass, or vinyl liner—will dramatically affect your budget, and understanding the cost variations is crucial for planning. This section breaks down the costs associated with each material, including essential components like pumps and filters.
Pool Shell Material Costs, Average cost of installing an inground outdoor pool
Concrete, fiberglass, and vinyl liner pools each offer unique advantages and disadvantages, reflected in their price tags. Concrete pools, known for their customization options and longevity, typically represent the highest upfront cost. Fiberglass pools, pre-fabricated and offering quicker installation times, fall in the mid-range price bracket. Vinyl liner pools, the most budget-friendly option, offer a good balance of affordability and aesthetics, though they require liner replacements over their lifespan.
Premium options within each category, such as using specialized concrete finishes or higher-grade fiberglass resins, can significantly increase the cost. For instance, a concrete pool with intricate tile work and a custom coping design will be considerably more expensive than a standard concrete pool with basic finishing. Similarly, a fiberglass pool with a more elaborate design or premium color options will command a higher price.
Costs of Essential Pool Components
Beyond the pool shell itself, several essential components contribute significantly to the overall material costs. Pumps, filters, and plumbing systems vary widely in price depending on their size, efficiency, and brand. High-efficiency pumps and advanced filtration systems, while more expensive upfront, can lead to long-term savings on energy and maintenance. Conversely, opting for basic, less-efficient models will reduce the initial cost but may increase operational expenses over time.
The plumbing system, including pipes, fittings, and valves, also contributes to the overall material cost, with variations depending on the materials used (e.g., PVC vs. more expensive, corrosion-resistant options). For example, a high-end pump system with variable speed capabilities might cost several hundred dollars more than a standard single-speed pump, but could significantly reduce energy consumption over the life of the pool.
Material Cost Comparison Table
Material | Average Cost Range | Lifespan Estimate | Premium Material Example & Increased Cost |
---|---|---|---|
Concrete | $30,000 – $80,000+ | 50+ years | Hand-laid tile, custom coping: +$5,000 – $20,000+ |
Fiberglass | $20,000 – $45,000 | 25-30 years | High-end resin, intricate design: +$5,000 – $10,000 |
Vinyl Liner | $15,000 – $30,000 | 9-12 years (liner replacement) | Thicker, more durable liner: +$1,000 – $3,000 |
Permits and Inspections
Navigating the permitting process for an inground pool is a crucial, and often overlooked, aspect of the overall project. Securing the necessary permits and passing inspections can significantly impact both the timeline and the final cost of your pool installation. Understanding the associated expenses and potential delays is essential for realistic budgeting and planning.Permitting fees vary widely based on your location and the specifics of your pool project.
Building an inground pool? Expect to shell out a pretty penny – the average cost can range widely depending on size and features. Of course, once it’s in, you’ll need to maintain it properly, which means keeping the chemicals balanced; check out this guide on how to balance pool chemicals without using test strips to save money on testing supplies.
Proper chemical balance is key to extending the life of your expensive new pool, so it’s a worthwhile investment of time and effort.
Factors such as the size of the pool, its features (e.g., a diving board, slide, or spa), and the complexity of the installation all influence the cost. Additionally, local government regulations and fees differ significantly from state to state, and even from county to county within the same state. Some jurisdictions may charge a flat fee, while others base their fees on the estimated project cost or the square footage of the pool.
Permit Fees and Variations
Permit fees are typically non-refundable, regardless of whether the project proceeds or is canceled. For example, a simple residential pool in a smaller town might cost between $500 and $1,500 for all necessary permits. However, a larger, more complex project in a densely populated area with stricter regulations could easily exceed $3,000. These fees often cover the administrative costs of processing the application, conducting site inspections, and ensuring compliance with building codes and safety regulations.
Obtaining permits often requires multiple submissions of paperwork, including detailed plans and specifications, and this process can be time-consuming.
Permit-Related Delays and Cost Impacts
Delays in obtaining permits are unfortunately common. These delays can stem from incomplete applications, missing documentation, revisions required by the reviewing authority, or simply a backlog of applications at the permitting office. Each delay translates into additional expenses. Contractors often charge holding fees or have to reschedule their crews, leading to increased labor costs. Material costs may also increase if prices fluctuate during the delay.
For instance, a two-month delay due to permit issues could easily add several thousand dollars to the overall project cost.
Common Permit Requirements
It’s crucial to understand the common requirements for inground pool installation permits. These requirements aim to ensure the safety and structural integrity of the pool and its surrounding area. The specific requirements may vary by location, but a typical list includes:
- Site Plan: Detailed drawings showing the pool’s location, dimensions, and proximity to property lines, structures, and utilities.
- Engineering Drawings: Structural plans demonstrating the pool’s design and construction methods, including the foundation, walls, and coping.
- Contractor Licensing: Proof that the contractor is properly licensed and insured to perform the work.
- Fence Requirements: Plans showing the type, height, and location of the required safety fence around the pool.
- Environmental Impact Assessment (in some cases): A study to evaluate the potential environmental effects of the pool construction.
- Compliance with Building Codes: Documentation demonstrating that the pool design and construction meet all applicable local building codes and safety regulations.
Additional Costs and Considerations: Average Cost Of Installing An Inground Outdoor Pool
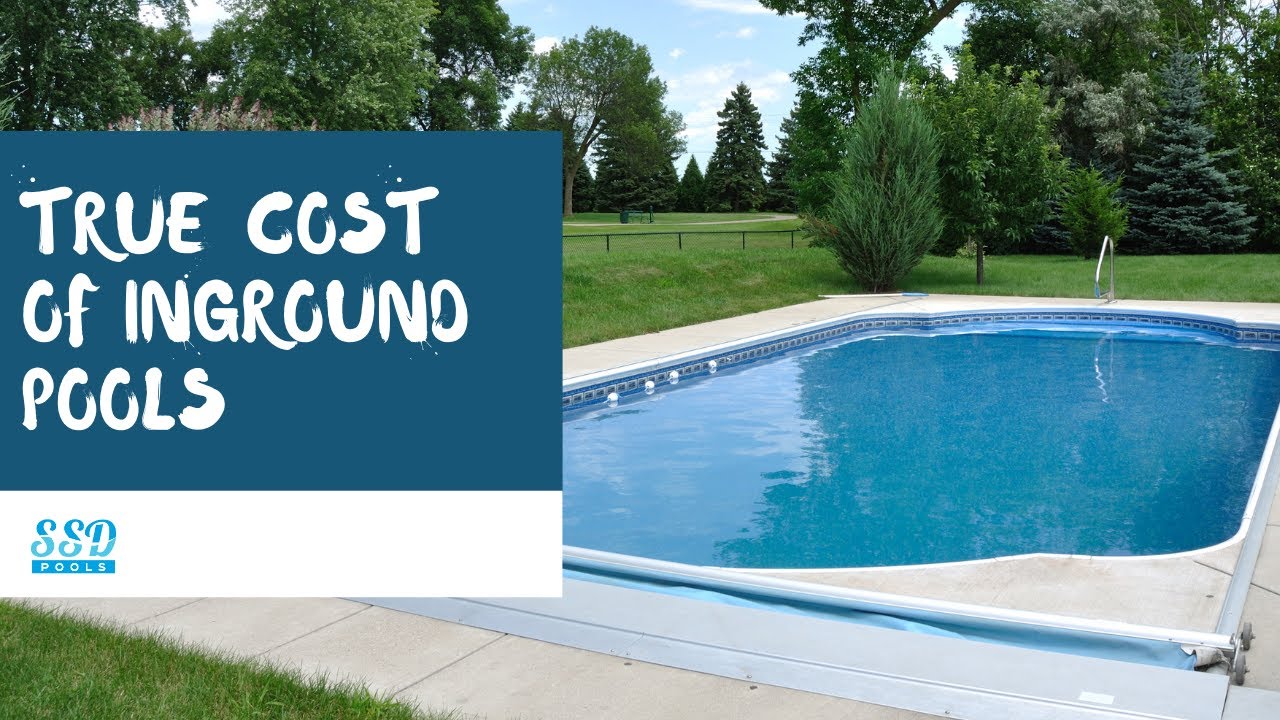
Source: ytimg.com
Building an inground pool is a significant investment, and the initial quoted price often doesn’t encompass the full financial picture. Homeowners need to account for several additional expenses to create a realistic budget and avoid unpleasant surprises during the project. Failing to plan for these extra costs can lead to project delays, budget overruns, and even compromise the overall quality of the finished pool.Beyond the core costs of pool construction, several other expenses can significantly impact the total project cost.
These additional expenditures often fall outside the scope of the initial pool contractor’s quote, highlighting the importance of proactive budgeting and contingency planning. Understanding these potential added costs allows for more informed decision-making and prevents financial strain during and after the project.
Landscaping, Fencing, and Electrical Work
Landscaping around the pool is crucial for aesthetics and safety. This might include grading the surrounding area, adding plants, and creating pathways. Fencing is often a legal requirement to ensure child safety, and the cost will depend on the type of fencing chosen (e.g., wood, vinyl, aluminum). Electrical work is essential for pool lighting, pumps, and other equipment.
For example, a homeowner might need to upgrade their electrical panel to handle the increased load or install a dedicated subpanel specifically for the pool. These costs can easily range from $5,000 to $20,000 or more, depending on the scale and complexity of the work. A simple, small pool might require less landscaping and a less extensive fence, whereas a larger, more elaborate pool with extensive lighting features will necessitate greater expense in these areas.
Building an inground pool is a big investment; the average cost can range widely depending on size and features. A significant portion of that cost often involves the heating system, so it’s wise to research your options before committing. Check out this helpful guide for a comparison of outdoor pool heating systems comparison and reviews to make an informed decision.
Ultimately, understanding heating costs will give you a more accurate picture of your total inground pool expense.
Unforeseen Expenses and Contingency Planning
Unforeseen expenses are almost inevitable in any large-scale construction project. Unexpected issues like rocky soil requiring extra excavation, unforeseen plumbing problems, or the discovery of underground utilities can significantly increase costs. For instance, hitting an underground rock formation during excavation could necessitate specialized equipment and significantly increase labor costs. Similarly, discovering a problem with existing plumbing that needs to be repaired before pool installation can add thousands of dollars to the project.
To mitigate these risks, a contingency fund is crucial. A common recommendation is to allocate 10-20% of the total estimated project cost as a contingency buffer. This reserve can absorb unexpected expenses without derailing the entire project.
Calculating Realistic Total Project Cost
Calculating a realistic total project cost involves more than just adding up the initial pool quote. It requires a detailed breakdown of all anticipated expenses, including:
- Pool Construction: This is the base cost from the contractor’s quote.
- Landscaping: Include costs for grading, sodding, planting, and pathways.
- Fencing: Factor in materials, labor, and permits for pool fencing.
- Electrical Work: Account for upgrades, new circuits, and installation of pool equipment.
- Permits and Inspections: Include all necessary fees and inspection costs.
- Contingency: Allocate 10-20% of the total estimated cost as a contingency fund.
For example, let’s say the initial pool quote is $50,000. Adding $10,000 for landscaping, $5,000 for fencing, $3,000 for electrical work, $2,000 for permits, and a 15% contingency ($11,250) results in a total estimated project cost of $81,250. This more comprehensive approach provides a more accurate reflection of the overall investment.
A realistic budget is essential for a successful and stress-free pool installation.
Visual Representation of Cost Breakdown
Understanding the cost breakdown of an inground pool installation is crucial for budgeting and planning. A typical breakdown involves several key components, each contributing a different percentage to the overall project cost. This section will illustrate a sample cost breakdown using a visual representation and detailed explanation.A common cost distribution for an average-sized inground pool project might look like this: Materials account for approximately 35-40% of the total cost, labor represents 30-35%, permits and inspections contribute around 5-10%, and the remaining 15-20% covers miscellaneous expenses like site preparation, additional features (like landscaping or decking), and unforeseen contingencies.
These percentages can vary significantly depending on factors like pool size, location, chosen materials, and complexity of the design.
Pie Chart Illustrating Cost Breakdown
To visualize this cost breakdown, consider a pie chart. The chart would be divided into four main segments: Materials, Labor, Permits & Inspections, and Other Costs.The largest segment would represent Materials (35%), depicted as a light blue slice. Next, the Labor segment (30%) would be shown as a slightly smaller, dark blue slice. The Permits & Inspections segment (8%) would be a small, green slice.
Finally, the remaining segment representing Other Costs (27%) would be a yellow slice. The percentages are approximate and can vary based on the specific project details. The chart title should clearly state “Inground Pool Installation Cost Breakdown.” Each slice should be clearly labeled with its corresponding cost category and percentage. The chart’s legend should also be included for easy interpretation.
The visual should be clean, easily readable, and professionally presented. This type of chart provides a quick and effective way to grasp the relative proportion of each cost element in a typical inground pool installation.
Outcome Summary
Building an inground pool is a significant investment, but the reward – a personal oasis for relaxation and entertainment – is undeniable. By carefully considering the factors discussed – materials, labor, permits, and potential extras – you can approach the project with confidence and create a budget that aligns with your vision and financial capabilities. Remember, thorough planning is key to a successful and enjoyable pool installation process.
So dive in and start planning your dream pool!
FAQ Corner
What’s the average lifespan of different pool materials?
Concrete pools typically last 50+ years with proper maintenance. Fiberglass pools usually last 25-30 years, while vinyl liner pools need replacement every 5-9 years.
Can I finance an inground pool?
Yes, many lenders offer financing options specifically for home improvements, including pool installations. Check with your bank or credit union for available options.
How much does pool maintenance cost annually?
Annual maintenance costs vary, but expect to spend several hundred dollars per year on chemicals, cleaning, and minor repairs.
What about insurance? Will my homeowner’s insurance cover a pool?
Most homeowner’s insurance policies will require an endorsement or a separate policy to cover a pool. Contact your insurance provider for details.
Are there energy-efficient options for pool heating?
Yes, consider heat pumps or solar heating systems to reduce energy costs associated with pool heating.